Case Studies
Kiln Fan Motor Bearing Defect
Request A Callback
Introduction
Malt Industry Kiln Fan
This case study is from one of our customers in the malt industry. One of the important process when creating malt is kilning. Kilning reduces the malts moisture and stops germination. Part of the kilning process involves large kiln fans to provide air flow to the kilns. At this customer their GKV fans are the most critical assets on site and failure on any fan or motor drive will directly impact production downtime. The fans are very big machines that are belt driven. Any catastrophic failure on a motor or a fan bearing will result in thousands of pounds downtime and huge repair costs.
Motor Bearing Defect
Striving to keep condition monitoring simple and effective
Detect
This kiln fan was located on the 4th floor of the kiln building. The location made it very difficult to replace the motor with the spare available. The motor was a 300KW Siemens N compact, this motor retails at £15,000.00 on around a 4-week lead time.
Using vibration analysis we were able to identified an inner race defect from motor on the non-drive end bearing. This was identified after our envelope acceleration reading triggered the critical alarms. An envelope acceleration reading is used to help identify metal to metal contact often caused by a bearing defect.
Using our analysis software we are able to overlay the inner race defect frequencies for the bearing, which in this case was an SKF 6218. Once overlayed we were now very confident of an outer race problem with this bearing. Due to the rapid rate of change we advised the customer to change the non-drive end bearing. At maintain our engineers are trained in precision bearing replacement and we worked with the customer to pick a window to change the bearing.
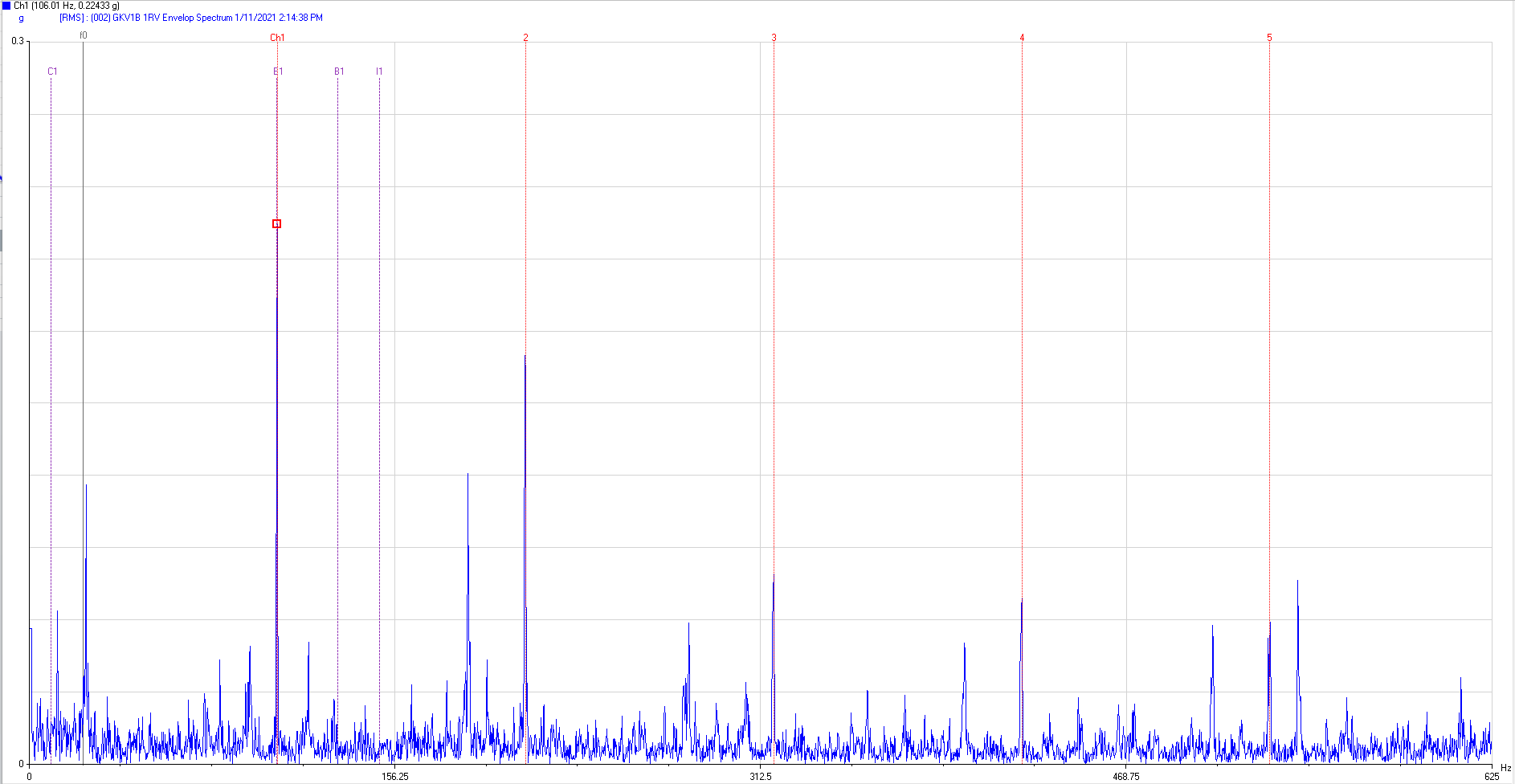
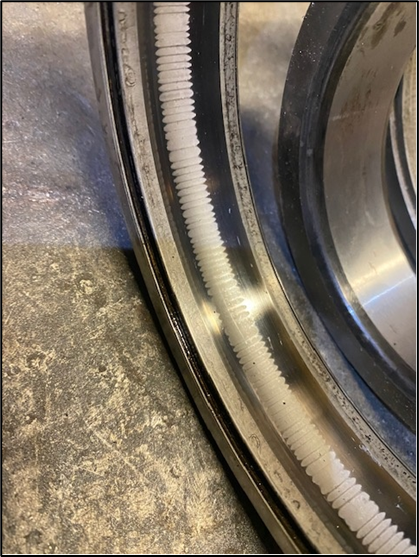
Solve
It is very common with motors than operate using an inverter to suffer from fluting also known as electro discharge machining (EDM). This can be very damaging to the motor bearings.
It the kilning processes the speed of the fan varies, from the cooling and heating of the malt through its different stages of production and therefore these fans operate on a inverter. It was important that we gather further information to conclude if EDM damage might be ocurring.
Using our Helwig BPK-Probe we are able to measure the shaft current and voltage. This enables us to see if the voltage or current is high enough to cause damage or reduced bearing life. During this test we were able to confirm the values were above the safe thresholf of operastion.
For this reason, we decided with the customer to instal an insulated bearing for the non-drive end. Usually, this type of bearing is installed to prevent circulating current but does not always solve the problem. From common mode current problems we install a shaft grounding device this adds another layer of protection for the bearings.
Solve
It is very common with motors than operate using an inverter to suffer from fluting also known as electro discharge machining (EDM). This can be very damaging to the motor bearings.
It the kilning processes the speed of the fan varies, from the cooling and heating of the malt through its different stages of production and therefore these fans operate on a inverter. It was important that we gather further information to conclude if EDM damage might be ocurring.
Using our Helwig BPK-Probe we are able to measure the shaft current and voltage. This enables us to see if the voltage or current is high enough to cause damage or reduced bearing life. During this test we were able to confirm the values were above the safe thresholf of operastion.
For this reason, we decided with the customer to instal an insulated bearing for the non-drive end. Usually, this type of bearing is installed to prevent circulating current but does not always solve the problem. From common mode current problems we install a shaft grounding device this adds another layer of protection for the bearings.
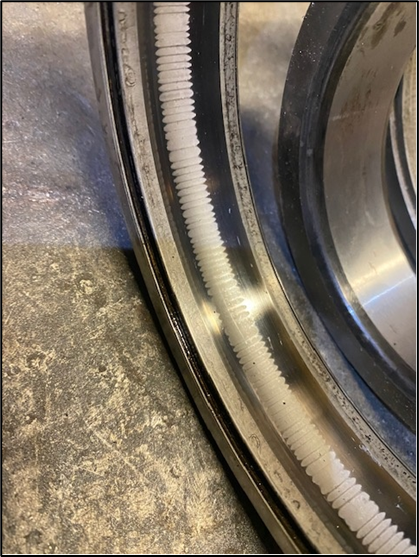
Improve
Working with our customer during there shutdown window we were able to change the non-drive end bearing. We removed the bearing using SKF hydraulic pullers to make sure that the bearing was removed cleanly without any damage. This was sent away for analysis. The shaft was cleaned, prepared and inspected before the new bearing was installed using an induction heater.
As seen in the pictures above the bearing has suffered from flutting due to electrico discharge machining. We also identified the bearing had been over lubricated. During the bearing change we calculated the grease quantity and applied this to the bearing after it had been installed and cooled.
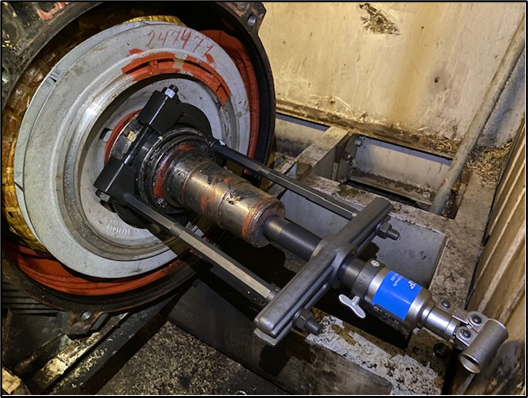
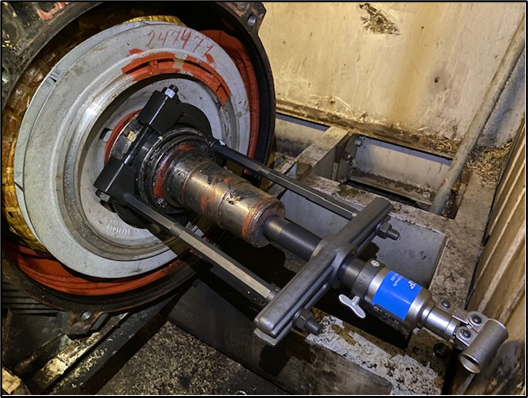
Improve
Working with our customer during there shutdown window we were able to change the non-drive end bearing. We removed the bearing using SKF hydraulic pullers to make sure that the bearing was removed cleanly without any damage. This was sent away for analysis. The shaft was cleaned, prepared and inspected before the new bearing was installed using an induction heater.
As seen in the pictures above the bearing has suffered from flutting due to electrico discharge machining. We also identified the bearing had been over lubricated. During the bearing change we calculated the grease quantity and applied this to the bearing after it had been installed and cooled.
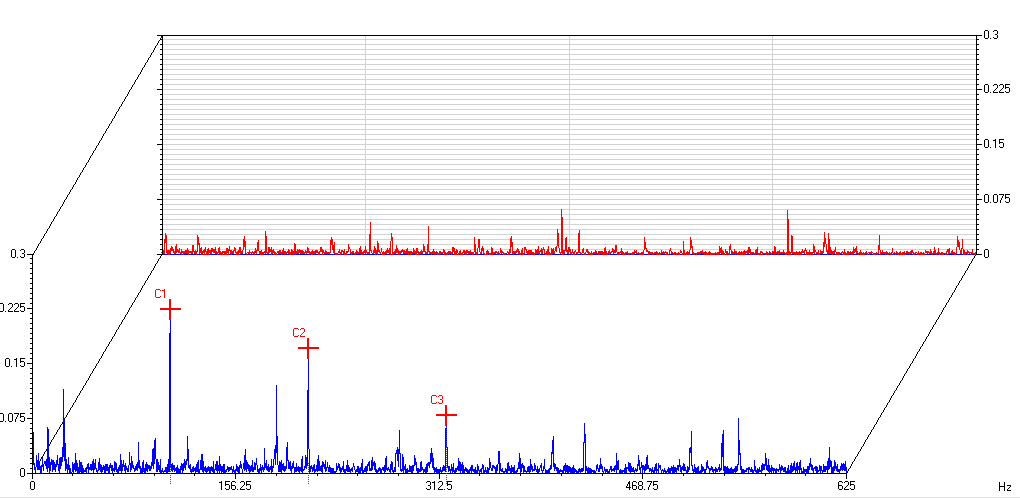
Conclusion
After the kiln was re-started we collected vibration data to make sure the bearing was operating correctly and that the lubrication level was adaquate. The data showed a fall in envelope readings after the bearing replacement and the shaft testing device voltage at a safe operating level.
Prior to the installation of an insulated bearing and the shaft grouding device this motor bearing was requring a replacement on average every 8 months. With these improvements made we hope to have greatly extended the life and reliability of this asset.
We have also taken over the greasing of this asset and base our levels on condition of the asset using high frequency vibration readings. This allows us to keep the bearing at an optimal level of grease so it cannot be over or under lubricated and enables the engineering team to focus on more important tasks.
Failure to identify this problem would have resulted in a possible catastrophic failure with an estimated downtime of 18 hours. We were able to calculate with our customer that the estimated loss of production would equate to £4000.00 per hour which could of resulted in a total cost avoidance of £72,000.00
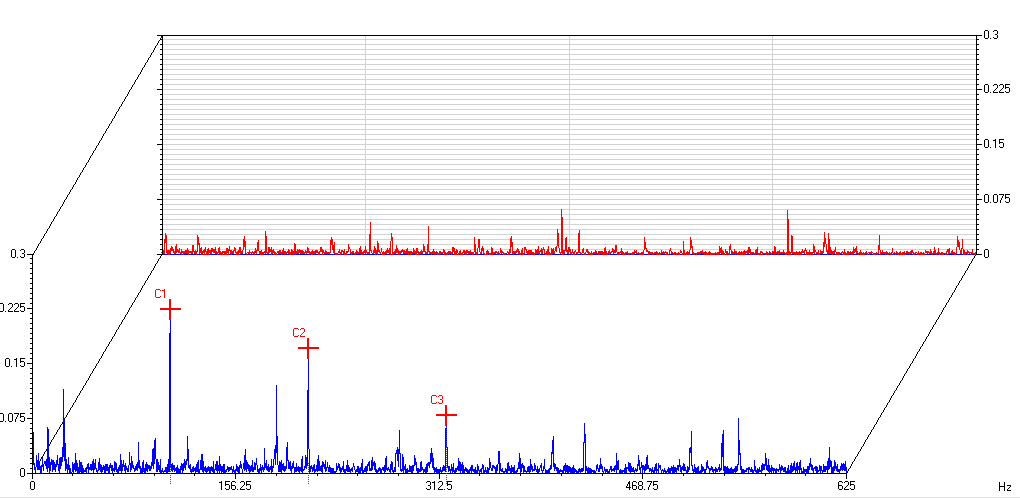
Conclusion
After the kiln was re-started we collected vibration data to make sure the bearing was operating correctly and that the lubrication level was adaquate. The data showed a fall in envelope readings after the bearing replacement and the shaft testing device voltage at a safe operating level.
Prior to the installation of an insulated bearing and the shaft grouding device this motor bearing was requring a replacement on average every 8 months. With these improvements made we hope to have greatly extended the life and reliability of this asset.
We have also taken over the greasing of this asset and base our levels on condition of the asset using high frequency vibration readings. This allows us to keep the bearing at an optimal level of grease so it cannot be over or under lubricated and enables the engineering team to focus on more important tasks.
Failure to identify this problem would have resulted in a possible catastrophic failure with an estimated downtime of 18 hours. We were able to calculate with our customer that the estimated loss of production would equate to £4000.00 per hour which could of resulted in a total cost avoidance of £72,000.00