Case Studies
Lubrication Factor
Request A Callback
Introduction
Lubrication
One third of all bearings fail due to poor lubrication according to SKF’s article Bearing Damage and Failure Analysis. There are many factors that contribute to good lubrication practices but being able to lubricate a bearing with the exact quantity of grease has always been a challenge. This subsequently leads to unaccounted costs or labour due to premature bearings failure which if detected would not have happened.
Lubrication is an often-overlooked element of any maintenance strategy, and for this reason it is why we consider it to be one of the most important tasks. At Maintain Reliability Ltd, we have found that current methods of lubrication have can result in an inconsistent grease application method. Therefore, at Maintain believe we have found a simple way to accurately measure lubrication in a bearing and to be able to precisely lubricate it with the exact quantity of grease it requires.
Lubrication Methods
Schedule Based Lubrication
What we would consider to be a more traditional approach to lubrication is based on a schedule. This is when a bearing is lubricated on a regular basis, regardless of whether the bearing requires it. The amount of grease required is based on predetermined calculations. It is very easy with lubrication schedules for a bearing, whilst in between lubrication, to be above or below the optimal requirement for lubrication. Furthermore, it can be very difficult to know the correct amount of grease that is put in each period, and whether enough for the bearing to be in its optimal lubrication range.
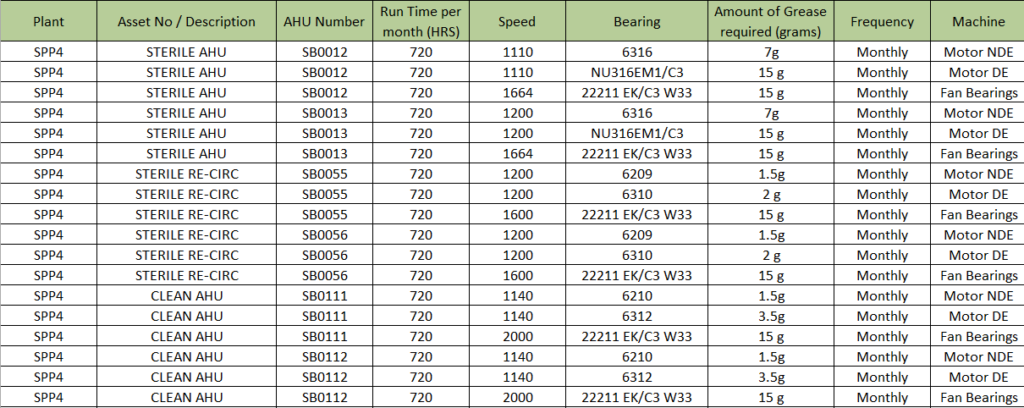
Lubrication with Ultrasound
Often used as an alternative to scheduled lubrication is ultrasound. This condition-based strategy uses ultrasound as a method to measure listen to a bearing. The data measuring at around 20Khz or above and a decibels value, is interpretated by the user. This can result in lubrication being given based on interpretation rather than a metric.
An individual’s experience of lubrication, knowledge of the bearings and machine as well as many other factors, contributes to how much grease is put into the bearing which can vary. Therefore, a reasonable level of experience is required when lubricating with ultrasound.
When using ultrasound, it is measuring at a much high frequency, therefore some may argue it is missing the fundamental frequencies which is presenting poor lubrication.
Another point is that the measurement range is not banded with ultrasound, as a result when listening, all events across the range can be heard. This can make the differentiation between the bearing itself or the state of lubrication difficult. In addition, when measuring the decibels level, the data can be affected by the speed, which produces data that could be misleading to an inexperience user. Overall, as a method of lubrication ultrasound can be used on some applications, but it can be inconsistent. It is not based on a specific metric and a reasonable level of experience is required.
Lubrication Factor - Acoem Falcon
The Acoem Falcon is an incredible analyser, on every asset we can measure up to 20Khz (1,200,000cpm) in under 10 seconds acquisition time. This is right on the edge of the ultrasound range. We have found that by using vibration analysis that it is possible to detect poor lubrication with vibration analysis. Previously considered not very effective.
When presented with a bearing we have conducted testing using the High Frequency Spectrum in the One Prod Falcon which is reading from 0 to 20Khz. We have identified within that range between 7500 Hz and 12,500 Hz (450,000cpm – 750,000cpm) poor lubrication presents itself in the data as haystack or raised floor. This is the frequency response of a dry race or poorly lubricated bearing.
When viewing the data In the High Frequency Spectrum we can take live readings and precisely grease the bearings until we see the haystack disappear and apply the correct amount of lubrication to reduce the friction within the bearing. This means that we do not have issues of under or over applying the grease to the bearing, which can later create problems.
At Maintain Reliability with have tested this method in the field at many different sites and have seen precise and effective results. So much so we have created a band alarm around 7500 Hz and 12,500 Hz, which allows us to create a metric measurement so that we can easily identify the haystacks and can very effectively identify poor lubrication and lubricate precise quantities of grease based upon a metric.
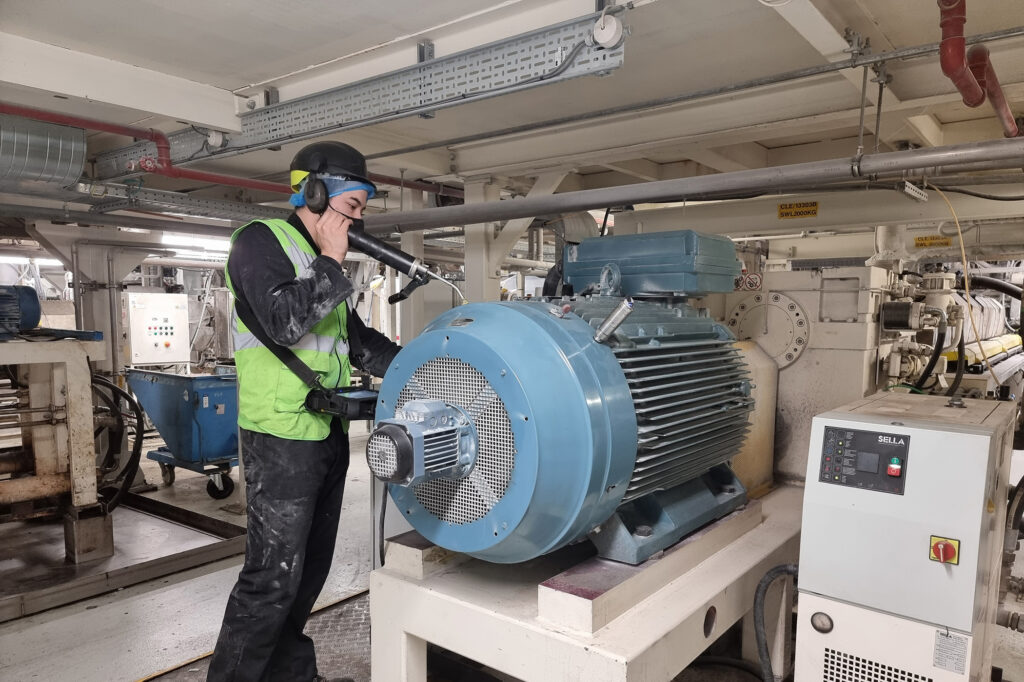
Case Study No.1
Biogas - Gas Booster Pump
Below are our findings from the alarms situated on a Gas Booster Pump from the Biogas Industry. We test a total of 8 Biogas sites across the UK. Each biogas site has 3 Booster Pumps, and we were consistently finding these to be under lubricated at all sites. Working with the maintenance team, we started using the falcon to precisely lubricate on each visit to make sure the bearing was staying in its optimal range during operation. Below is the data of lubrication before and after:
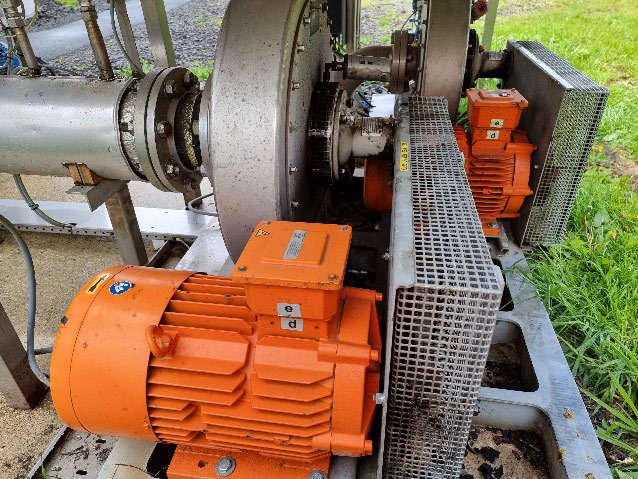
Vibration Alarms Before Lubrication

High Frequency Spectrum Before Lubrication
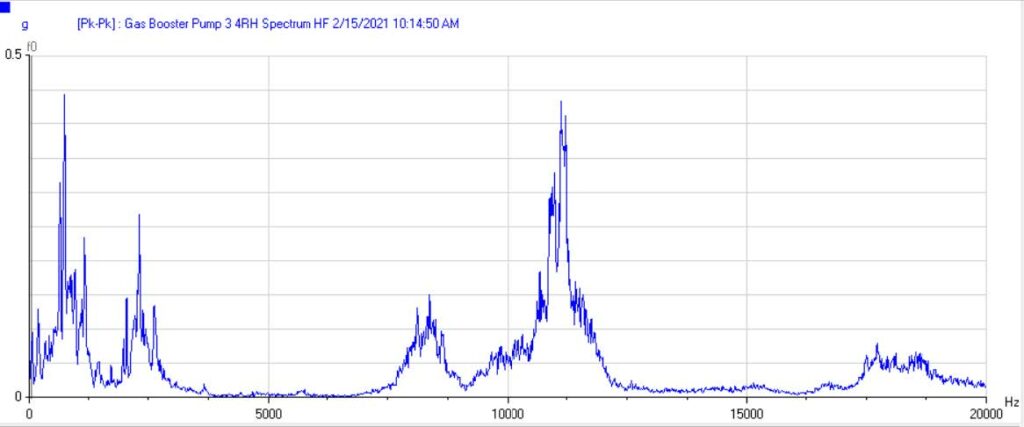
Vibration Alarms After Lubrication

High Frequency Spectrum After Lubrication
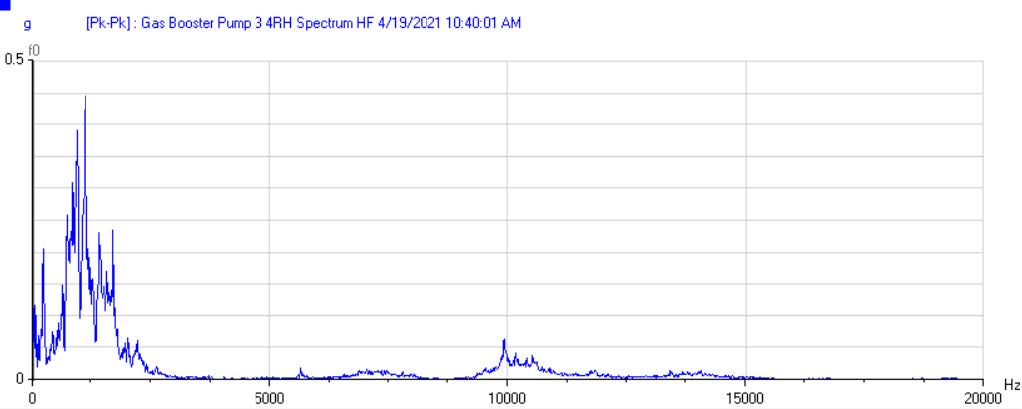
High Frequency Spectrum Before and After Overlayed
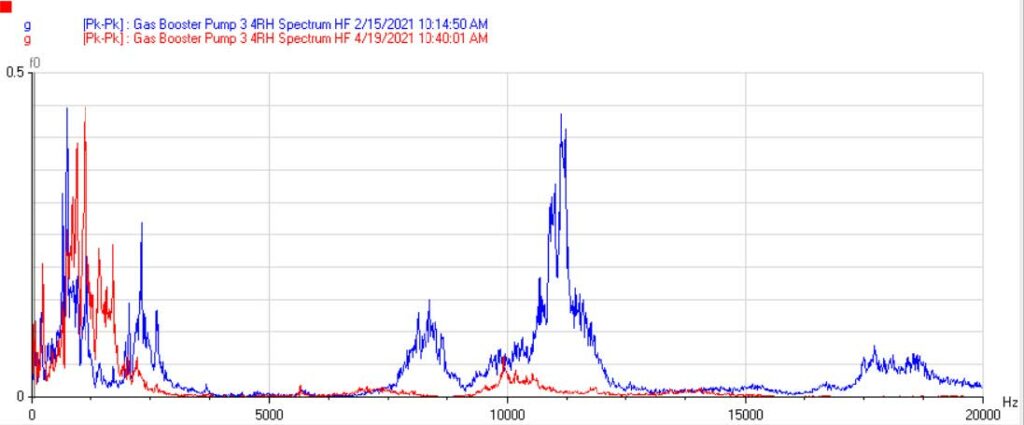
Lubrication Factor - Acoem Falcon
Lubrication factor can be set up with Nesti4.0 very quickly. Lubrication factor is a band alarm looking at the high Ffrequency spectrum which is set-up by default from Acoem. Below are all the settings information to try lubrication factor out for yourself. Our testing so far shows this reading to be more effective with the Acoem wireless sensor. We are still completing tests with various fixed sensors to further understand how this effects the Lubrication Factor reading.

High Frequency Spectrum
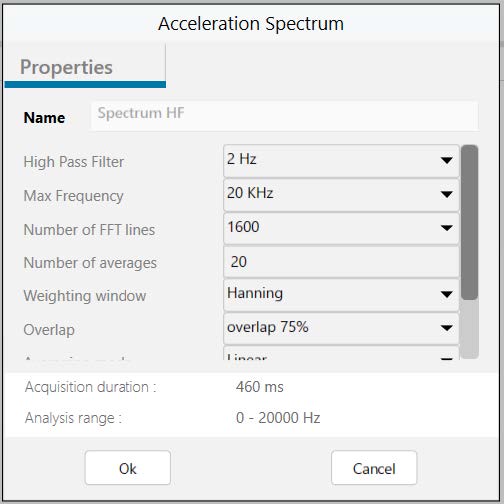
Lubrication Factor Alarm
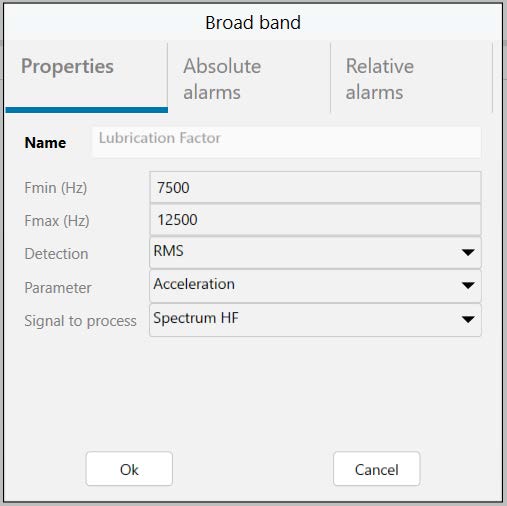
Case Study No.2
Food - Refrigeration Compressor
Below are the alarms placed on a Compressor Motor in the Food Industry. We provide asset care on these motors alongside the regular vibration analysis. Using Lubrication Factor, we can closely trend the lubrication value and lubricate as this begins to increase early before it goes into alarm. Previously this motor was in alarm for lubrication 80% of the time during our visits. With asset care and lubrication factor, we now maintain the lubrication film in its optimal level before it gets to low to cause any damage.
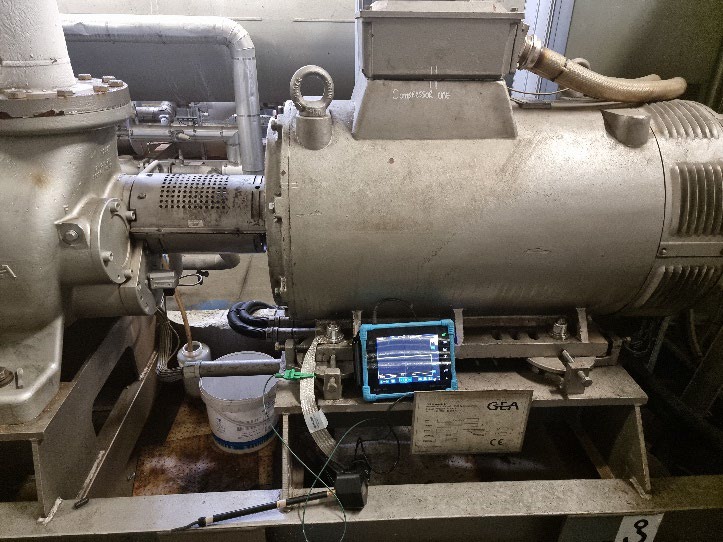
Vibration Alarms Before Lubrication
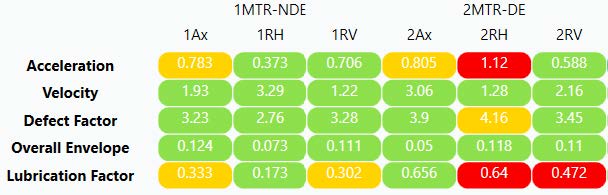
High Frequency Spectrum Before Lubrication
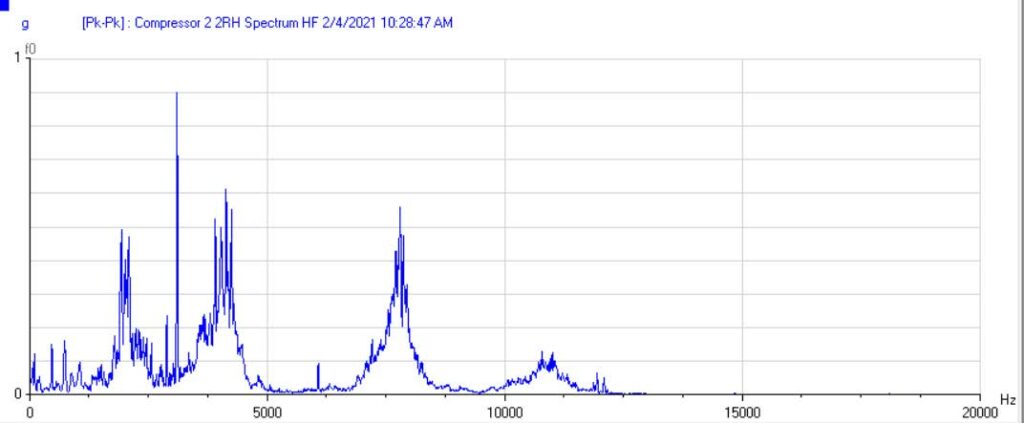
Vibration Alarms After Lubrication
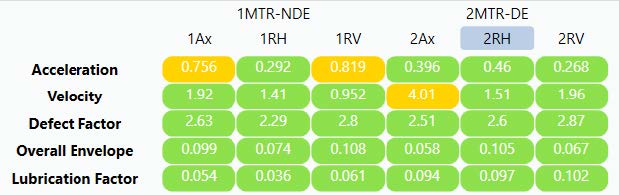
High Frequency Spectrum After Lubrication
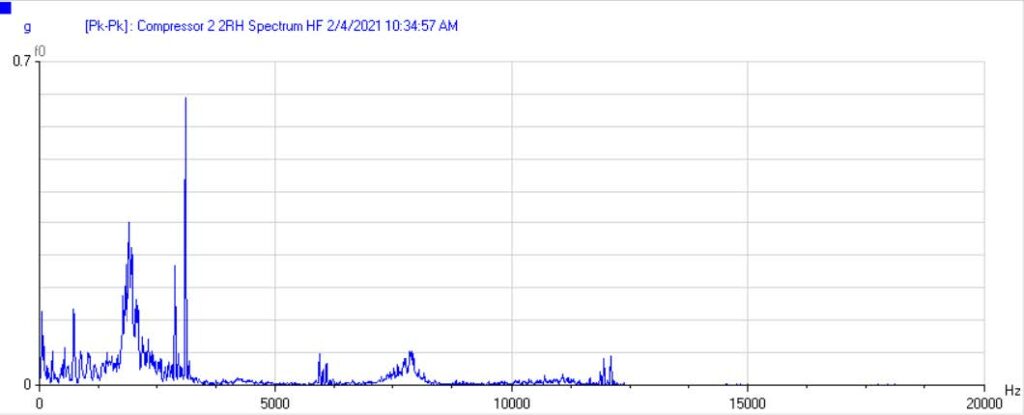
High Frequency Spectrum Before and After Overlayed
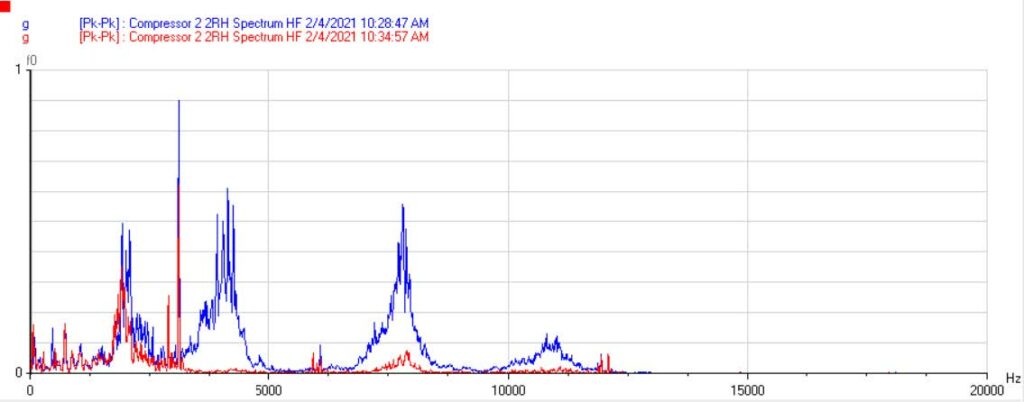
Conclusion
Lubrication Factor is always evolving with every site we go to, we learn more and develop this method of lubrication. By being able to simply apply the correct amount of grease to a bearing without hesitation is something us at Maintain Reliability Ltd feel solves many problems with current methods of lubrication and is a driect impact to the machines reliability. Our goal is to help reduce the amount of failures caused by poor lubrication and help companies be more cost sustainable and operate a reliable plant.